The Ultimate Guide To How Bullets Are Made: A Comprehensive Overview
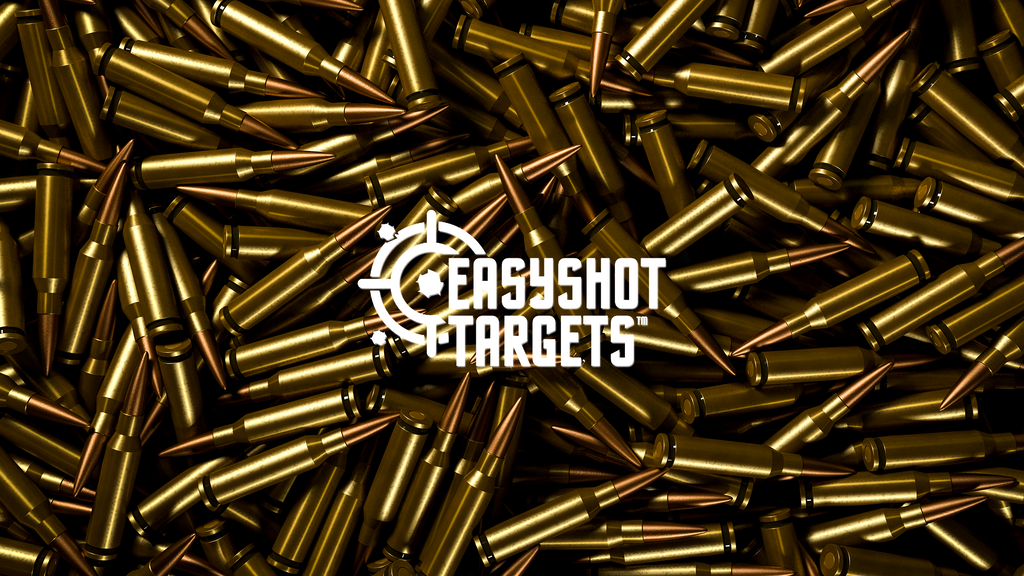
Introduction
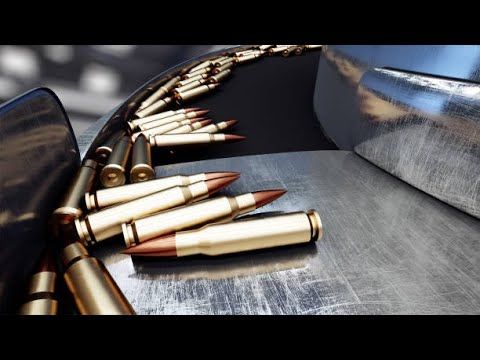
Have you ever wondered about the intricate process behind the manufacturing of bullets? From the raw materials to the final product, the journey of a bullet’s creation is fascinating and involves a combination of precision engineering and craftsmanship. In this comprehensive guide, we will delve into the world of bullet manufacturing, exploring the various steps, techniques, and considerations that go into producing these essential components for firearms. Whether you are a firearms enthusiast, a hunter, or simply curious about the science behind ammunition, this guide will provide you with an in-depth understanding of how bullets are made.
Understanding the Basics

Before we dive into the manufacturing process, let’s familiarize ourselves with some key concepts and terms related to bullets:
- Bullet: The projectile, typically made of metal, that is fired from a firearm.
- Caliber: The diameter of the bullet or the internal diameter of the firearm’s barrel. It is often measured in millimeters (mm) or hundredths of an inch.
- Cartridge: The complete ammunition package, consisting of the bullet, casing, primer, and propellant.
- Casing: The container that holds the primer, propellant, and bullet. It is usually made of brass, steel, or other materials.
- Primer: A small explosive charge that ignites the propellant when struck by the firing pin.
- Propellant: The chemical compound that produces gas when ignited, propelling the bullet forward.
The Manufacturing Process

Now, let’s explore the step-by-step process of how bullets are made:
Step 1: Raw Material Preparation
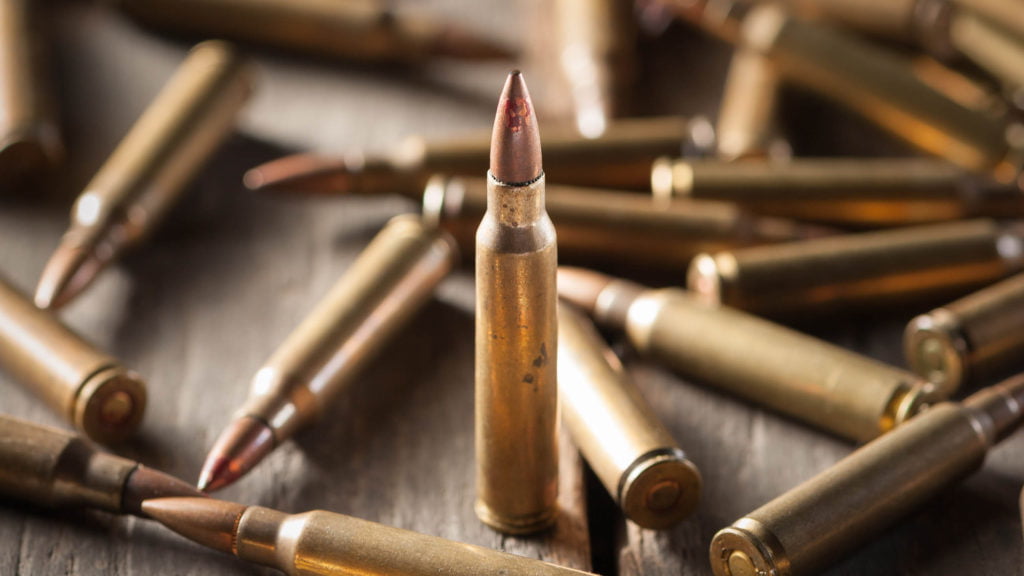
The first step in bullet manufacturing is acquiring and preparing the raw materials. The primary material used for bullet cores is typically lead, which is a soft and malleable metal. However, to improve performance and reduce environmental concerns, manufacturers often use lead alloys or alternative materials such as copper, brass, or steel.
The raw materials are carefully selected and tested to ensure they meet the required standards. Lead and its alloys are typically sourced from recycling processes, ensuring sustainability and minimizing environmental impact.
Step 2: Core Formation

Once the raw materials are prepared, the next step is to form the bullet cores. This process involves shaping the metal into the desired shape and size. There are several methods used for core formation:
- Casting: Molten metal is poured into molds to create bullet cores. This method is commonly used for lead bullets and allows for the production of various shapes and sizes.
- Swaging: A swaging machine is used to apply pressure to shape the metal into the desired form. This process is often used for smaller-caliber bullets and provides precise control over the core dimensions.
- Extrusion: Metal is forced through a die to create a continuous profile, which is then cut to length. This method is commonly used for larger-caliber bullets and offers high production efficiency.
Step 3: Jacket Preparation

For certain types of bullets, a jacket or coating is applied to the core to enhance performance and reduce lead exposure. The jacket material is typically a harder metal, such as copper or copper alloys, which provides better penetration and accuracy.
The jacket preparation process involves the following steps:
- Jacket Production: The jacket material is rolled and formed into thin sheets or strips.
- Annealing: The jacket material is heated to soften it and improve its workability.
- Cutting: The jacket material is cut into the required shape and size to fit the bullet core.
- Joining: The jacket is then carefully joined to the bullet core, ensuring a secure and precise fit.
Step 4: Assembly and Loading

With the bullet cores and jackets prepared, the next step is to assemble the components and load them into the cartridge cases. This process is highly automated and involves the following steps:
- Primer Insertion: Primers are placed into the base of the cartridge cases.
- Powder Charging: The correct amount of propellant is measured and loaded into the cartridge cases.
- Bullet Seating: The bullet, with or without a jacket, is seated into the cartridge case, ensuring a tight fit.
- Crimping: The cartridge case is crimped to secure the bullet in place and prevent any movement during firing.
- Inspection: Each loaded cartridge is carefully inspected to ensure quality and consistency.
Step 5: Quality Control and Testing

Quality control is a critical aspect of bullet manufacturing to ensure the final product meets the required standards and performs reliably. Various tests and inspections are conducted at different stages of the process:
- Dimensional Inspection: Bullet cores and jackets are measured to ensure they meet the specified dimensions.
- Weight Checking: The weight of the bullet and cartridge is verified to ensure consistency.
- Performance Testing: Loaded cartridges are fired to evaluate their performance, including accuracy, velocity, and penetration.
- Environmental Testing: Bullets may undergo tests to simulate real-world conditions, such as extreme temperatures and humidity.
Types of Bullets
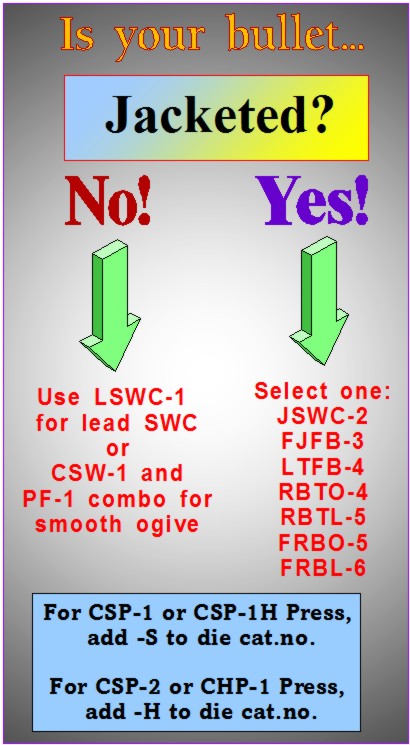
Bullets come in various shapes, sizes, and designs, each serving specific purposes and offering unique advantages. Here are some common types of bullets:
- Full Metal Jacket (FMJ): These bullets have a solid metal jacket encasing the lead core, providing excellent penetration and accuracy. FMJ bullets are commonly used for target practice and plinking.
- Jacketed Hollow Point (JHP): JHP bullets have a hollow cavity in the tip, which expands upon impact, increasing stopping power. They are widely used for self-defense and hunting applications.
- Soft Point (SP): SP bullets have a softer lead core exposed at the tip, offering a balance between penetration and expansion. They are popular for hunting medium to large game.
- Ballistic Tip: Ballistic tip bullets feature a plastic tip that enhances aerodynamic performance and accuracy. They combine the benefits of both FMJ and JHP bullets.
- Frangible: Frangible bullets are designed to break apart upon impact, minimizing the risk of over-penetration. They are often used for training and in situations where bullet fragmentation is desirable.
Safety Considerations
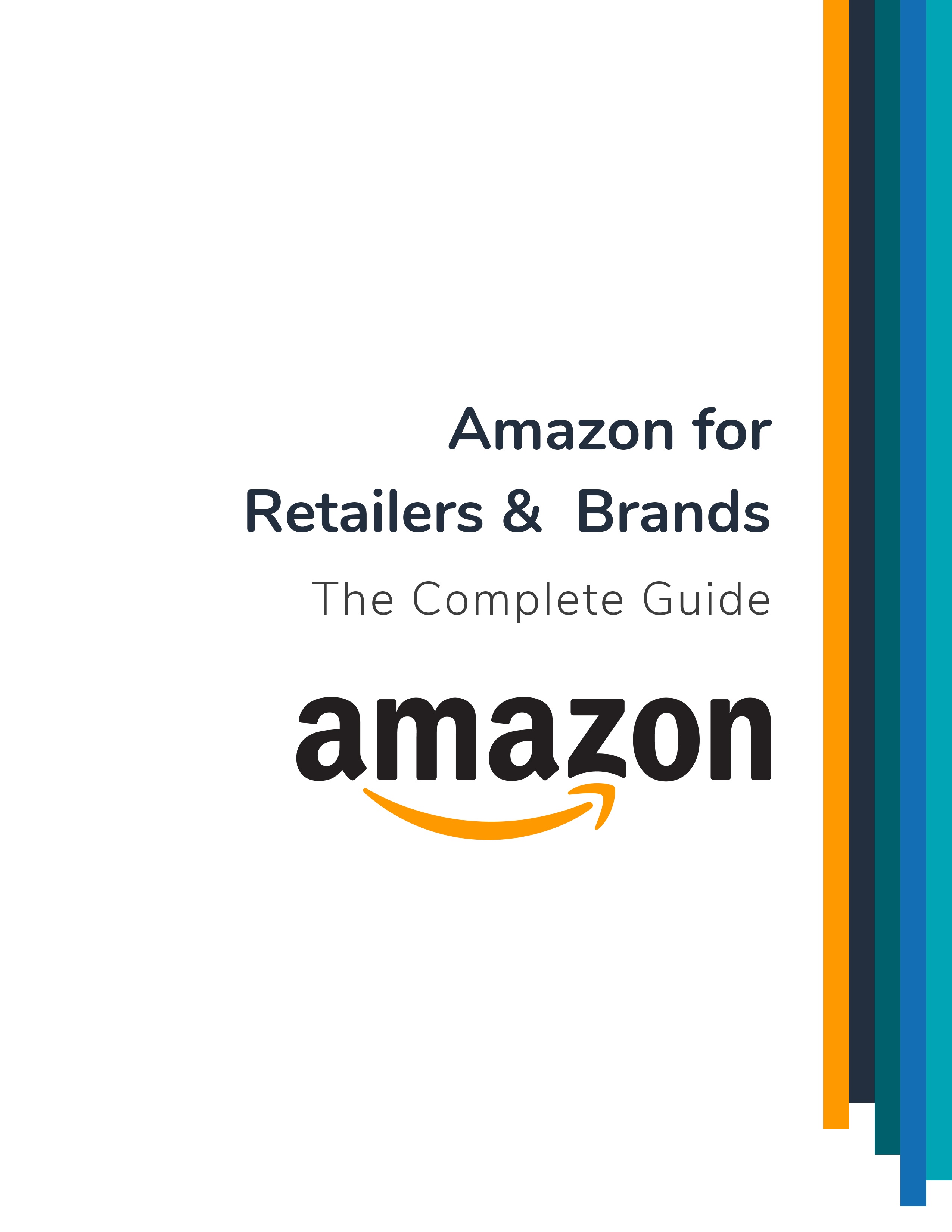
Bullet manufacturing, like any industrial process, comes with certain safety considerations. Here are some key points to keep in mind:
- Lead Exposure: Lead is a toxic metal, and proper precautions must be taken to minimize exposure during the manufacturing process. This includes the use of personal protective equipment (PPE) and proper ventilation systems.
- Fire Hazards: The presence of flammable materials and explosive components requires strict adherence to safety protocols to prevent fires and explosions.
- Noise Levels: The manufacturing process can generate high noise levels, and hearing protection is essential for workers.
- Environmental Impact: Bullet manufacturers are increasingly focusing on sustainable practices and reducing the environmental impact of their operations. This includes recycling lead and implementing eco-friendly materials and processes.
Frequently Asked Questions (FAQ)

What is the most common material used for bullet cores?

+
The most common material used for bullet cores is lead. However, due to environmental concerns and performance considerations, manufacturers often use lead alloys or alternative materials like copper, brass, or steel.
How are bullet jackets applied to the core?
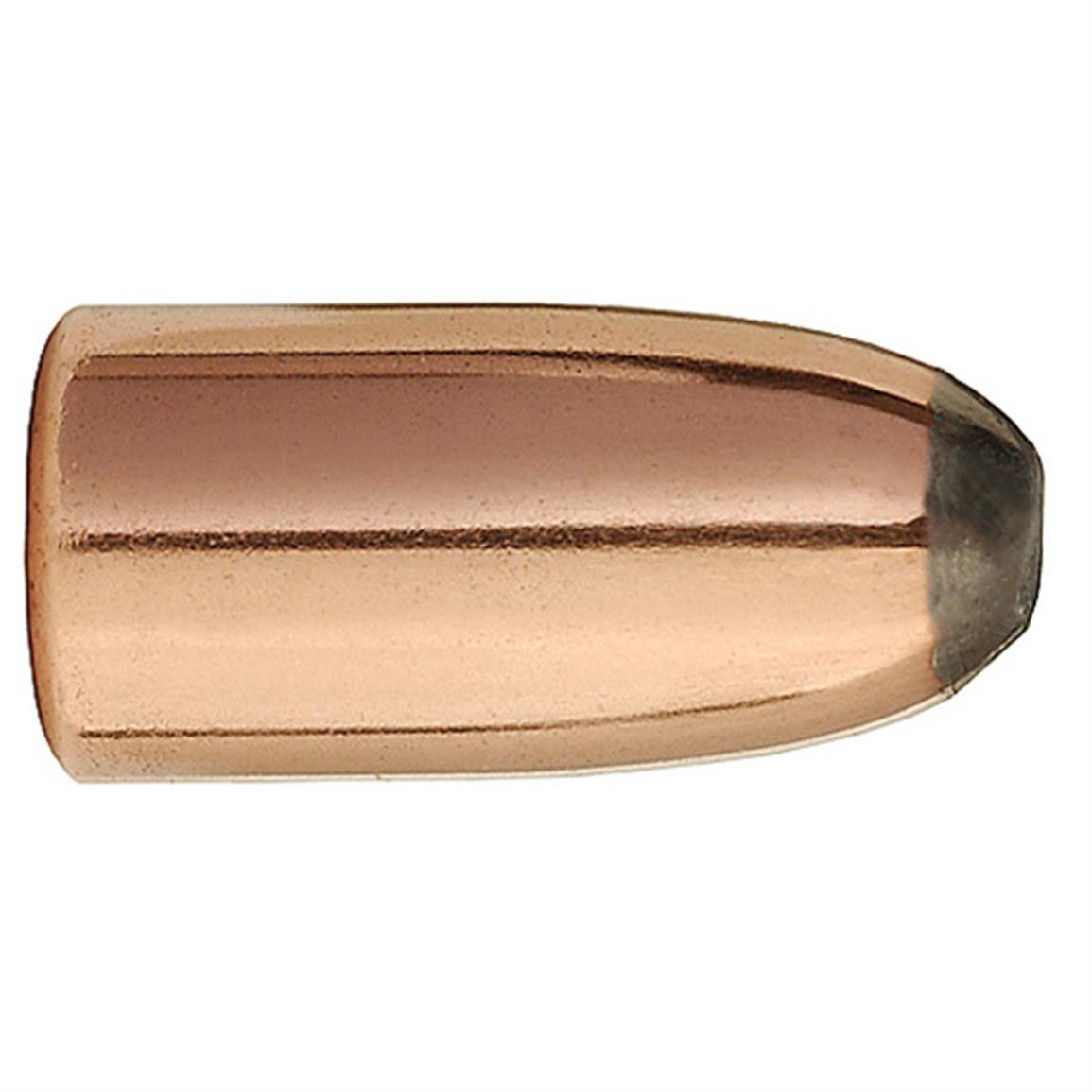
+
Bullet jackets are typically joined to the core through a process called swaging or crimping. This ensures a secure fit and prevents any separation during firing.
What are the advantages of frangible bullets?

+
Frangible bullets are designed to break apart upon impact, reducing the risk of over-penetration. They are ideal for training scenarios and situations where minimizing collateral damage is crucial.
Final Thoughts

Understanding the intricate process of bullet manufacturing provides us with a deeper appreciation for the precision and craftsmanship involved in creating these essential components. From the selection of raw materials to the final quality control checks, each step contributes to the reliability and performance of bullets. Whether you are an avid shooter, a hunter, or simply interested in the science behind ammunition, this guide has hopefully provided valuable insights into the world of bullet manufacturing. Remember to always prioritize safety and responsible practices when handling firearms and ammunition.